Magnetic Tape Deterioration, Part 1: Magnetization & Base Damage (October 2022, updated December 2023)
Since launching Play It Again, Paul, I’ve encountered several reel-to-reel tapes in less-than-optimal condition. While most were playable, though occasionally with minor distortion, others had deteriorated to the point of major distortion, physical damage to the tape, and loss of audio. In this pair of articles, I’ll be addressing primarily reel-to-reel tapes, since problems are encountered most frequently with this medium. Cassettes are not immune, but incidence is less frequent, and issues have received less attention. This article describes problems associated with magnetization and with damage to the base (or substrate—the flexible strip that gives the tape body and upon which other layers are applied) and concludes with recommendations for slowing deterioration. Part 2 addresses tapes’ binder (a coating that holds the magnetizable and lubricating particles in place) and back coating (a layer opposite the binder that reduces static electricity and provides additional lubrication).
Magnetization
Print-Through
Tapes store audio content in magnetizable oxide or metal particles called domains. Domains are not only magnetized during recording, but they can also be unintentionally altered by other magnetic sources. An unavoidable source, known formally as thermo-remanent magnetization, is the magnetization that tape will absorb from adjacent layers of tape on a reel. The result, print-through, is that one can hear not only the tape’s original audio content but also content from a few inches away at the same time. Unfortunately, this begins taking effect immediately after a recording is made. When it reaches audible levels depends on the amount of time that has elapsed, exposure to high temperatures during storage, thickness of the base, stability of the magnetic particles, the speed at which the tape was recorded, and the difference in volume between the original and print-through content. There’s no way to remove print-through content, though it can be minimized in places where the original content is silent.
Several authorities suggest that print-through can be countered by winding the tape onto another reel and storing it “tail up” for an extended period. Each layer of tape will be adjacent to different sections with different content, and as print-through inevitably begins again, the effect is to counteract the original print-through content.
My perspective on this is that the net result would be thermo-remanent magnetization acquired from two separate layers of tape resulting in accumulated noise—not an improvement. Personally, I dislike this practice since the tape ends up on a reel likely to have different brand markings than the original, thereby removing a clue of the tape’s true brand (and possibly a label on the reel indicating the tape’s content).
Cassettes are also subject to thermo-remanent magnetization. A significant portion of a collection of commercially produced cassettes I converted in a recent project suffered from print-through, which substantially increased the effort to achieve satisfactory noise reduction.
External Magnetization
A second type of damage is anhysteretic magnetization, which occurs when a tape is placed within an external magnetic field. Magnetization picked up from external sources can be as strong as that of the original signal, and removal of the resulting audio noise may not be possible. This problem is somewhat infrequent since most people using tapes are typically careful about accidental exposure. I store all magnetic media—especially my customers’—several feet away from any electronic devices and their cables, electrical wires including those in my walls, electric motors, computers, and CRT monitors and televisions (when I still had some). Though I haven’t seen any specific warnings regarding flat-screen monitors and televisions or wireless phone chargers, I’m cautious in avoiding these devices as well.
It is difficult to ascribe a tape’s noise specifically to the recording environment, the recorder’s transport mechanism, deficiencies in the recorder’s conversion of the electronic signal into magnetization, or anhysteretic magnetization since they can sound very similar. A recent project involved a particularly noisy tape where the speaking tempo slowed and pitch decreased as the recording progressed, indicating it was made on a recorder that used the take-up reel as the transport mechanism rather than a capstan. After applying a progressive speed change to the audio file, I obtained a recording with constant tempo and pitch, but it resisted my typical broadband noise reduction approaches.
Inspecting the recording’s spectrograms before and after making the speed change (Figures 1 and 2, respectively), I discovered a band of high-frequency noise that was uniform before the speed change but exhibited a gradual increase in frequency after the change. If that noise had been caused by any of the factors occurring when the recording was made, the noise should have had the opposite pattern: gradually decreasing frequency before the speed correction and uniform frequency after the correction. This was a clear indication (the only one I’ve seen, actually) that the noise was a result of anhysteretic magnetization. Broadband noise reduction assumes that the noise to be removed is consistent throughout the recording, which is why it had failed. Applying broadband noise reduction to the original recording and then applying the progressive speed change facilitated my efforts at noise reduction.
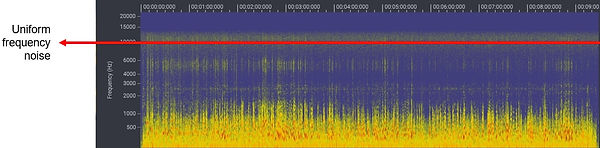
Figure 1. Spectogram of uniform frequency noise.
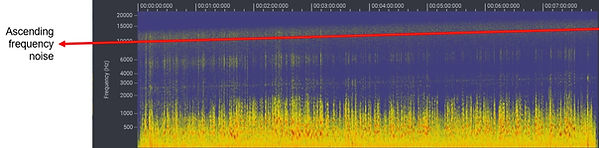
Figure 2. Spectogram of ascending frequency noise.
Base Damage
There are several types of substrate damage that will affect playability and audio quality. Some can occur immediately as a tape is being played or develop more slowly over multiple playings. Others, caused by storing tapes in high temperature and, especially, high humidity conditions, can take years to emerge.
Base Material
The material comprising the base is an important factor. Acetate was the most prevalent substrate into the late 1960s, as it satisfied strength, stability, and flexibility requirements. Polyethylene terephthalate (I’ll refer to this simply as “polyester”) tapes first appeared in the 1950s, but it wasn’t until the late 1960s that polyester overtook acetate as the material of choice. Production of acetate audio tapes ceased in the early 1970s. There were two reasons for the industry shift to polyester: less susceptibility to many of the kinds of damage listed below, and an oxide formulation that allowed for a greater dynamic range (the difference between the highest and lowest amplitudes that the medium could capture and reproduce). Some acetate tape manufacturers adopted polyester’s oxide formulation for the final years of their tapes’ production.
Tape boxes typically specified the base material: acetate (sometimes called “plastic”) or polyester (frequently using Mylar or Tenzar brand names). If you encounter a tape whose box does not specify the base or a tape that is no longer in its original box, you should be able to figure out the base material by holding the tape up to a bright light source. You can see light coming through acetate tape (Figure 3) but not through polyester tape (Figure 4). (The pack should be tightly wound; otherwise, you may see light coming through a reel of polyester tape because of the loose pack.)

Figure 3. A backlit 5” reel of acetate tape.

Figure 4. A backlit 5” reel of polyester tape.
Stretching
Base materials can withstand longitudinal stretching up to 5% of the original length; its elasticity permits return to about the original length. If a tape is stretched more than 5%, the audio will exhibit slower tempo and lower pitch than it should. Depending on the severity of the stretch, the width may become narrower, and the tracks may no longer line up with the playback head. In severe cases, the tape will turn into an unplayable filament. (It takes 20% less force to stretch an acetate tape to the point where it’s permanently damaged than that affecting polyester tapes.)
-
Causes: Take-up reel using excessive winding force, excessive drag by the supply reel, contraction resulting from a significant drop in temperature after a tape has been wound tightly. Though rare, stretching can also occur because of improper threading or an improperly applied splice catching on a head, tape guide, or tape lifter. (Since my tape deck was engineered to accommodate 7” and 10.5” reels, excessive supply reel drag is evident with 3” and 5” tapes. To circumvent this effect, I transfer smaller tapes to 7” reels before conversion.)
Cupping: A tape’s base and binder layers expand and contract at different rates. This results in small waves in the tape (known as cupping), which can interfere with uniform contact against the tape deck’s recording and playback heads. Audio quality is compromised. (Acetate tapes’ cupping is much more pronounced than that of polyester tapes.)
-
Causes: Large changes in humidity and temperature.
Wind Stability and Humidity
“Wind stability” refers to how tightly tape is wound into the pack on a reel during playing, fast-forwarding, or rewinding. Ideally, a pack will be tight enough to avoid shifting as the reel is held in different positions, but not tight enough to risk stretching the tape. Unfortunately, acetate tape will become loose when exposed to high humidity, leading to layers of tape abrading their adjacent neighbors. Conversely, acetate tape will become tight in very low humidity, and the resulting stress can distort the tape, again affecting audio quality. (Polyester tapes are much more stable and do not exhibit these changes )
-
Causes: High and low humidity, recurring significant changes in temperature or humidity.
Wind Stability and Tape Transport
When a tape is wound onto a reel, the results should be a snug pack in the shape of a uniform cylinder with no edges sticking out from the pack (known as frilling), and with no puckering or bunching up into peaks within the pack. Too tight a wind risks stretching the tape, and too loose a wind will allow the tape to shift position between the flanges (pack slip), abrading the tape, damaging edges, and occasionally catching on a flange during playback. Another issue with a loose wind occurs when parts of a tape stored horizontally sag away from the pack, which can cause the tape to become wavy longitudinally. This is known as country laning because the tape can wander back and forth across heads perpendicular to the direction of tape travel.
-
Causes: Take-up reel winding with more force than it should, excessive or inadequate drag on the supply reel during fast-forwarding or on the take-up reel during rewinding, reel tables out of alignment (reel tables are the circular platforms that turn as a tape is being played; tapes are anchored on spindles in the center of the tables), misaligned or damaged tape guides.
Aging
The acetate substrate contains a plasticizer that can dry out over time, resulting in the tape becoming brittle. Moisture can be reintroduced into the base by suspending an affected tape over water or by storing the tape in its box with lightly dampened cotton balls in the box’s corners. Though these measures will improve the condition of an old tape, they will not restore it to its original conditions. (This problem does not occur with polyester tapes because the base does not contain a plasticizer.)
-
Cause: Low humidity.
Breakage
Several factors can lead to a tape’s breaking, such as excessive supply reel drag or take-up reel force, and of course aging. Edges exposed by frilling are subject to partial breaks in the form of slits or nicks (see Figure 5). These weaken the tape, and it will eventually break where slits or nicks appear.
-
Causes: Reel table out of alignment resulting in tape scraping against the reel flange, loose tape pack, mishandling, failed or improper splices, crumpled tape ends where the tape has been threaded onto a reel . (I have had to deal with acetate tapes that break into several 1” segments because of crumpling; attaching additional leader reduces the risk of this breakage.

Figure 5. Pronounced nick in the edge of a tape.
Vinegar Syndrome
Under certain conditions, acetate interacts with iron oxide particles in the binder and decomposes into acetic acid, giving off a vinegar smell. This was primarily noticed in the film industry, where acetate-based film is stored in metal cans. Storage of acetate tapes in cardboard boxes and providing ventilation significantly retard the vinegar syndrome. (Polyester tapes do not contain acetate and thus are not subject to this type of deterioration.)
-
Causes: High temperature and humidity and storage in a metal can.
Recommendations for Preserving Your Tapes’ Audio
To minimize further deterioration of your tapes, I recommend the following steps.
-
Transfer your recordings to a digital format. Since many types of damage are irreversible, and the likelihood of damage increases over time, this must be my first recommendation, particularly for acetate tapes.
-
Store polyester tapes in a constant, moderate temperature (50⁰ to 75⁰ F.), low humidity (30% to 45% relative humidity) environment and away from any electromagnetic fields or heat sources, preferably in air-tight containers (better brands of polyester tape come in a round plastic container that fits within the typical cardboard tape box). Some authors consider 65⁰ and 40% relative humidity to be ideal conditions.
-
Store acetate tapes in cardboard boxes in a constant, moderate temperature, moderate humidity environment and away from any electromagnetic fields or heat sources.
-
Store tapes vertically, not flat.
-
Apply a preservative specially formulated for audio tapes, but only after you have determined that they are suffering from coating deterioration (addressed in Part 2).
-
Maintain your tape deck, including reel table alignment, supply reel drag, take-up reel force, and head alignment.
Part 2 of this series addresses deterioration of the binder layer and back coating.
Back to Paul’s Blog & Contents